
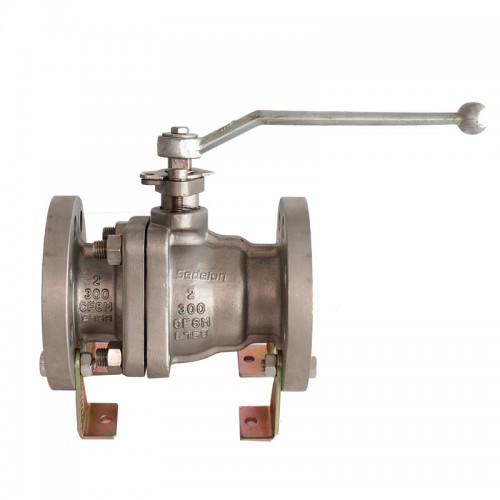
Product overview
3D casted end entry and side entry soft-seated floating ball valves are designed according to ISO17292. These valves are usually applied in low pressure systems (150~300LB) with a wide temperature range (-46℃~200℃). The valves are fire safe designed and have been certified per API607 and API6FA. 3D range consists of one-piece end entry and two-piece split body designs.
Size:1/2"~10"(DN15~DN250)
Pressure Rating: ASME CLASS 150~300(PN16~PN40)
Body material:Carbon steel, Stainless steel, Alloy steel, Duplex stainless steel,exotic alloy etc.
End connection:FLNG, BW
Operation:Manual, Pneumatic, Electric, Hydraulic,ect.
Advantages and disadvantages of ball valve
1、 Advantages:
(1) It has the lowest flow resistance (actually 0);
(2) Because it will not get stuck during operation (when there is no lubricant), it can be reliably used in corrosive media and low boiling point liquids;
(3) Complete sealing can be realized in a large pressure and temperature range;
(4) It can realize rapid opening and closing, and the opening and closing time of some structures is only 0.05 ~ 0.1s, so as to ensure that it can be used in the automation system of the test-bed. When the valve is opened and closed quickly, the operation has no impact.
(5) The spherical closing part can be automatically positioned at the boundary position;
(6) The working medium is reliably sealed on both sides;
(7) When fully open and fully closed, the sealing surface of the ball and valve seat is isolated from the medium, so the medium passing through the valve at high speed will not cause erosion of the sealing surface;
(8) With compact structure and light weight, it can be considered as the most reasonable valve structure for low temperature medium system;
(9) The valve body is symmetrical, especially the welded valve body structure, which can well bear the stress from the pipeline;
(10) The closing part can withstand the high pressure difference during closing.
(11) The ball valve with fully welded valve body can be directly buried underground, so that the valve internals are not corroded, and the maximum service life can reach 30 years. It is the most ideal valve for oil and natural gas pipelines.
2、 Disadvantages:
(1) Because the main valve seat sealing ring material of the ball valve is polytetrafluoroethylene, it is inert to almost all chemicals, and has the comprehensive characteristics of small friction coefficient, stable performance, not easy to aging, wide temperature application range and excellent sealing performance.
However, the physical characteristics of PTFE, including high expansion coefficient, sensitivity to cold flow and poor thermal conductivity, require that the design of valve seat seal must focus on these characteristics. Therefore, when the sealing material hardens, the reliability of the seal is damaged.
Moreover, the temperature resistance grade of polytetrafluoroethylene is low and can only be used under the condition of less than 180 ℃. Beyond this temperature, the sealing material will age. When considering long-term use, it will only be used at 120 ℃.
(2) Its regulation performance is worse than that of stop valve, especially pneumatic valve (or electric valve).
3、 Scope
Because the ball valve usually uses rubber, nylon and polytetrafluoroethylene as the seat sealing ring material, its service temperature is limited by the seat sealing ring material. The cut-off function of the ball valve is completed by mutual compression between the metal ball and the plastic valve seat under the action of the medium (floating ball valve).
Under the action of a certain contact pressure, the valve seat sealing ring has elastic-plastic deformation in some areas. This deformation can compensate the manufacturing accuracy and surface roughness of the ball and ensure the sealing performance of the ball valve.
In addition, since the valve seat sealing ring of the ball valve is usually made of plastic, the fire resistance and fire prevention of the ball valve should be considered in the selection of the structure and performance of the ball valve, especially in the petroleum, chemical, metallurgy and other departments, when the ball valve is used in the equipment and pipeline system of flammable and explosive media, more attention should be paid to fire resistance and fire prevention.
In general, ball valves are recommended for pipeline systems with two position adjustment, strict sealing performance, mud, wear, necking channel, rapid opening and closing action (1 / 4 turn opening and closing), high pressure cut-off (large differential pressure), low noise, cavitation and gasification, small leakage to the atmosphere, small operating torque and small fluid resistance.
The ball valve is also applicable to the pipeline system with light structure, low pressure cut-off (small differential pressure) and corrosive medium. Ball valves can also be used in low temperature (cryogenic) devices and pipeline systems. In the oxygen pipeline system of metallurgical industry, ball valves with strict degreasing treatment need to be used. When the main pipelines in oil and gas pipelines need to be buried underground, full-diameter welded ball valves need to be used.
When the regulation performance is required, the ball valve with special structure with V-shaped opening shall be selected. In petroleum, petrochemical, chemical, electric power and urban construction, metal to metal sealed ball valves can be selected for pipeline systems with working temperature above 200 ℃.