
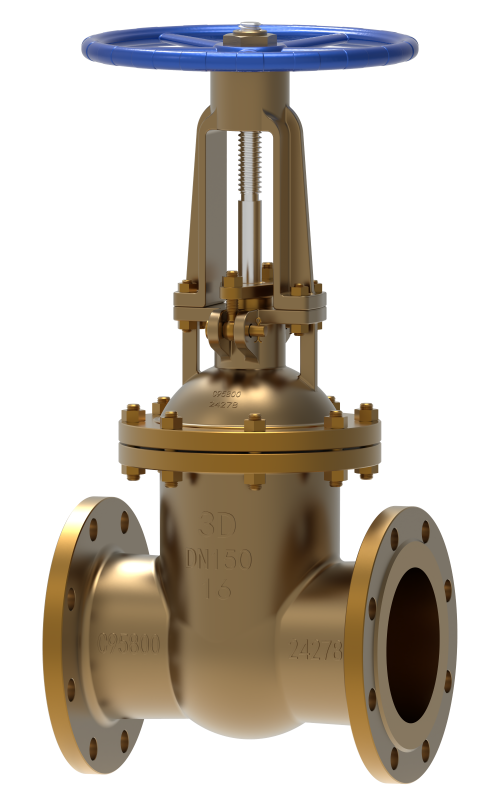
Introduction:
DIN standard gate valves are crucial components in piping systems, designed to control the flow of fluids in various industrial applications. The wear-resistant and corrosion-resistant variants of these valves are specifically engineered to withstand harsh environments where abrasion and corrosion pose significant challenges.
Features:
1. Wear-Resistant Materials: DIN standard gate valves are constructed using wear-resistant materials such as hardened stainless steel, chromium-molybdenum alloy, or ceramic coatings to withstand abrasive wear and prolong service life.
2. Corrosion-Resistant Coatings: These valves are equipped with corrosion-resistant coatings or linings, such as epoxy coatings or nickel-based alloys, to protect against chemical corrosion and extend the valve's lifespan.
3. Sturdy Construction: Wear-resistant and corrosion-resistant gate valves feature a robust construction, providing excellent strength and durability to withstand high-pressure and corrosive environments.
4. Rising Stem Design: These valves typically feature a rising stem design, allowing for visual indication of the valve's position and facilitating maintenance and repair.
5. Bolted Bonnet: The bolted bonnet design allows for easy access to internal components for maintenance and repair, enhancing the valve's serviceability.
6. Flanged Ends: DIN standard gate valves come with flanged ends for easy installation and connection to piping systems using bolted flange connections.
7. Non-Rising Stem Option: Some valves offer a non-rising stem option, suitable for applications with limited space or where underground installation is required.
8. Pressure Rating: These valves are available in various pressure ratings to suit different application requirements.
Working Environment:
Wear-resistant and corrosion-resistant DIN standard gate valves are suitable for a wide range of working environments, including:
1. Oil and Gas Industry: These valves are used in upstream, midstream, and downstream oil and gas operations for flow control in pipelines, refineries, and petrochemical plants where abrasive and corrosive fluids are present.
2. Mining and Mineral Processing: Gate valves are employed in mining and mineral processing operations for controlling the flow of abrasive slurries, tailings, and process fluids in various stages of the mining process.
3. Chemical Processing: These valves find applications in chemical processing plants for regulating the flow of corrosive chemicals, acids, and aggressive fluids used in manufacturing processes.
4. Water and Wastewater Treatment: Wear-resistant and corrosion-resistant gate valves are utilized in water treatment plants, wastewater treatment facilities, and desalination plants for controlling the flow of corrosive and abrasive fluids.
Working Principle:
1. Normal Operation: During normal operation, the gate of the valve is raised to allow fluid flow through the valve. The rising stem design provides visual indication of the valve's position, indicating whether the valve is open or closed.
2. Shut-off Operation: To shut off flow, the gate is lowered to its closed position, blocking the flow of fluid through the valve. The tight sealing provided by the gate ensures leak-free shut-off.
3. Pressure Resistance: The sturdy construction and wear-resistant materials used in these valves enable them to withstand high-pressure environments without compromising sealing performance or structural integrity.
4. Maintenance: Wear-resistant and corrosion-resistant gate valves require minimal maintenance due to their durable construction and corrosion-resistant coatings. Periodic inspections and lubrication of moving parts may be necessary to ensure optimal performance and longevity.